Production
Behind the historic walls of our factory in Nijverdal (NL), traditional textile processes and modern chemical processes intermingle. This is where the textile substrates are upgraded to functional outdoor products. Continuous improvement of the processes, quality and turnaround time of our products is in the genes of our operations departments. TenCate Outdoor Fabrics manages the entire process of substrate, pre-treatment and post-treatment.
Fabric, the substrate technology
The basis of our product is a textile substrate. TenCate has more than 300 years of experience in this technology. The textile process starts with a careful selection of fibres, which are spun into yarns in a 100% variant or intimate mixing by open end spinning technology. Subsequently, these yarns form the rough canvas in a flat (1/1), oxford (2/1) or panama (2/2) bond. Here, the density of the fabric, or the number of yarns in the warp and in the weft, is important for the strength, air permeability and water tightness of the end product.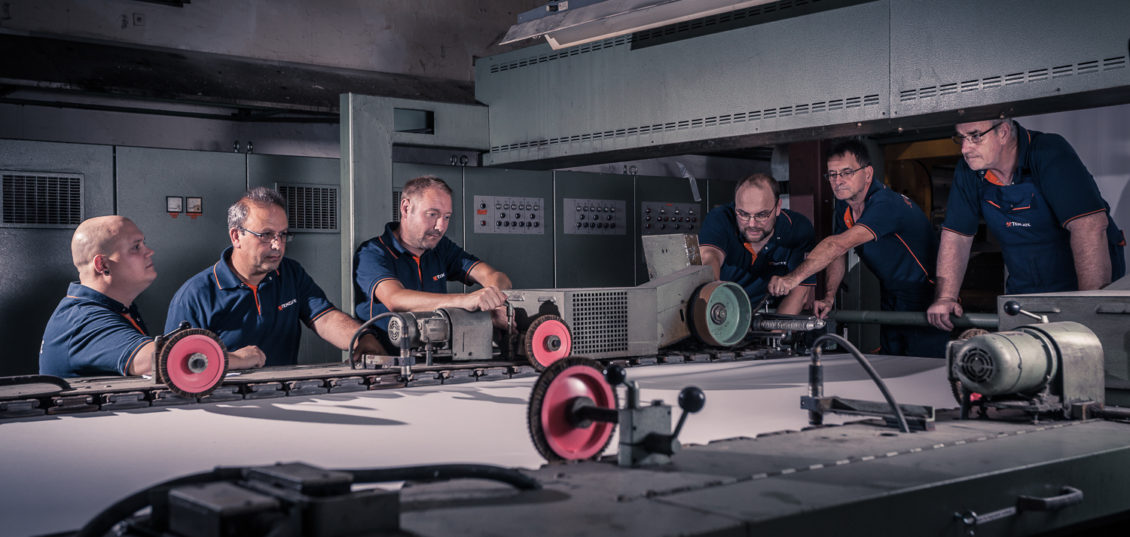
Pre-treatment of the fabric
The rough canvas must be treated further to guarantee a consistent quality. The canvas is washed and bleached and at a later stage moistened, stretched and stabilised in a fabric oven. After this process the canvas is ready to be dyed.
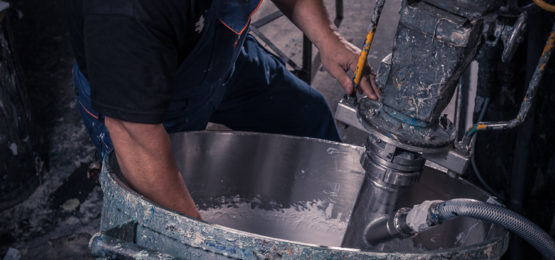
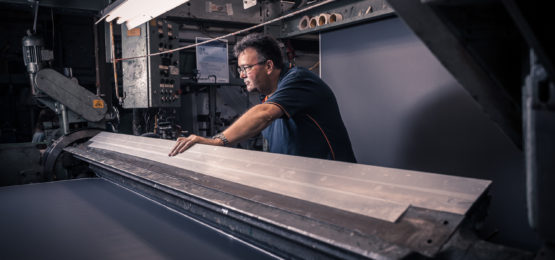
Post-treatment of the fabric
Following the dyeing process our Touring and Residential products are coated. Depending on the desired level of water repellency, colour effects and protection, one, two or three layers of coating are applied to the fabric.
TenCate also offers the possibility to print the fabric; in which advanced digital UV printing technology is used. The inks used are sustainable and the prints are of high quality with 800dpi.
The finish is a final protective layer and protects the fabric from contamination and provides a good repellent against raindrops.
On average, a canvas passes through the production line eight times before it is eventually inspected, rolled on tubes and packed.
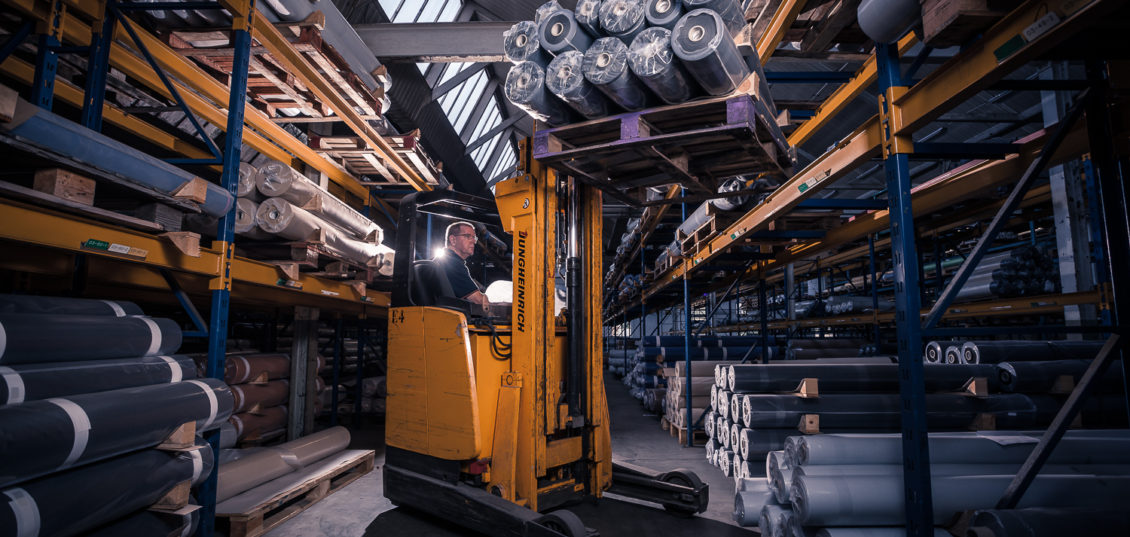